Takezawa Seiki’s one-pass honing can improve productivity and reduce costs in any situation that requires honing, regardless of the industry.
Inner diameter finish of Bearing parts after carburizing and quenching
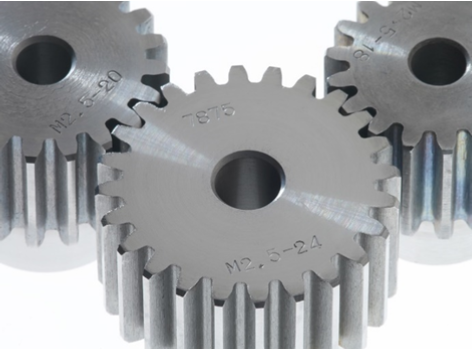
This is an example of finishing the inner diameter of a very hard material after carburizing and quenching. The heat treatment caused distortion of the inner diameter, which needed to be corrected. General tools were not efficient enough for this type of machining, so we used Takezawa Seiki’s CBN lapping reamer and floating holder. As a result, we were able to achieve the desired level of accuracy and meet our production volume.
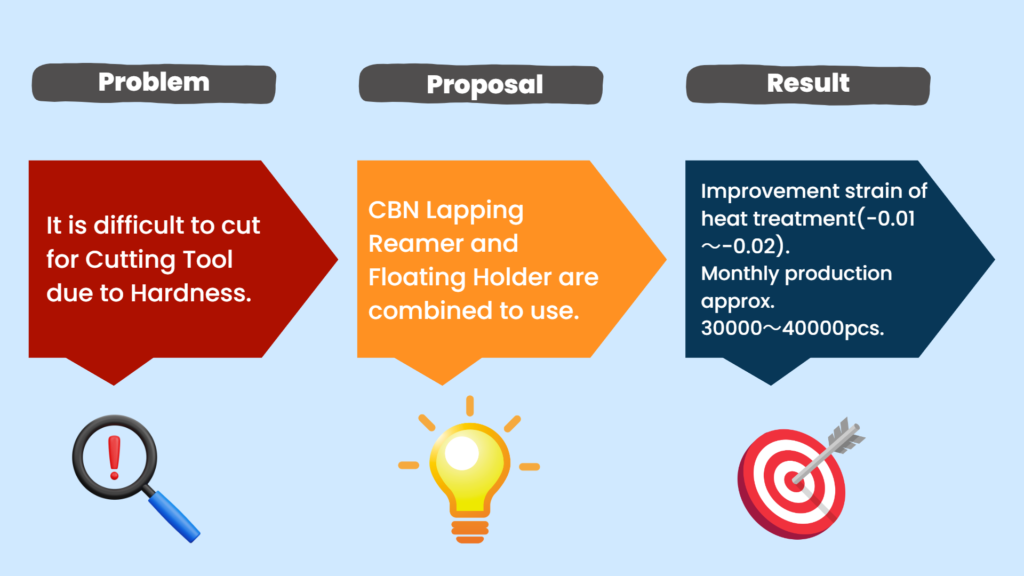
Productivity improvement through process consolidation
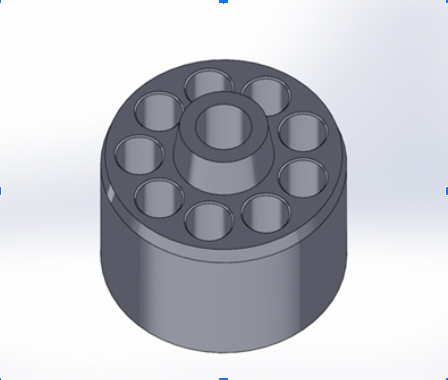
This is an example of how we reduced the time and effort needed for honing. In the past, honing was done in two separate stages: blank processing and honing. But by using Takezawa Seiki’s diamond reamer, we can now do both processes using a single machining center.
This has led to a reduction in setup time and an increase in productivity. Best of all, we achieved this process improvement without having to spend any additional money on equipment.
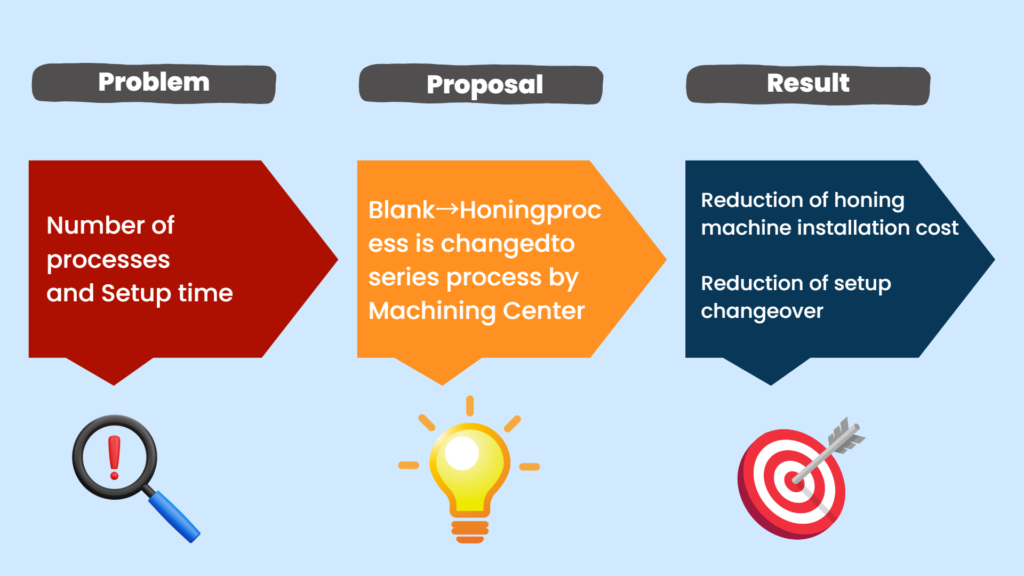
Improvement of cylinder surface roughness (Hydraulic equipment manufacturer)
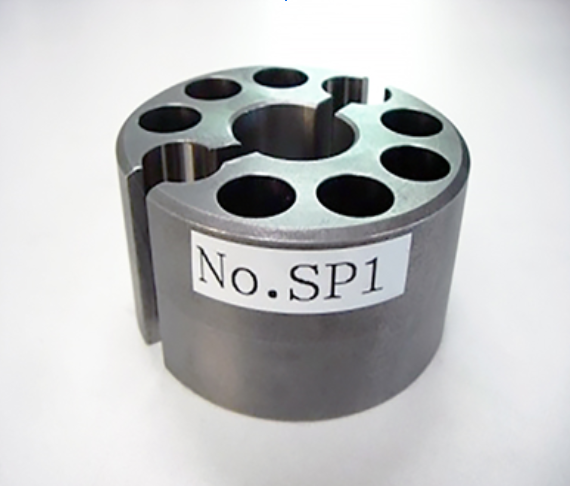
This is an example of how the honing process for hydraulic cylinders was improved. The unstable surface roughness resulted in poor yield and reduced productivity. After investigating the issue, it was discovered that the cause was the tool’s runout during processing. Takezawa Seiki proposed and provided their diamond reamer and floating holder, which were then adopted.
As a result, not only did the machining accuracy become stable, but a series of machining by the machining center became possible, reducing setup work and significantly improving productivity.
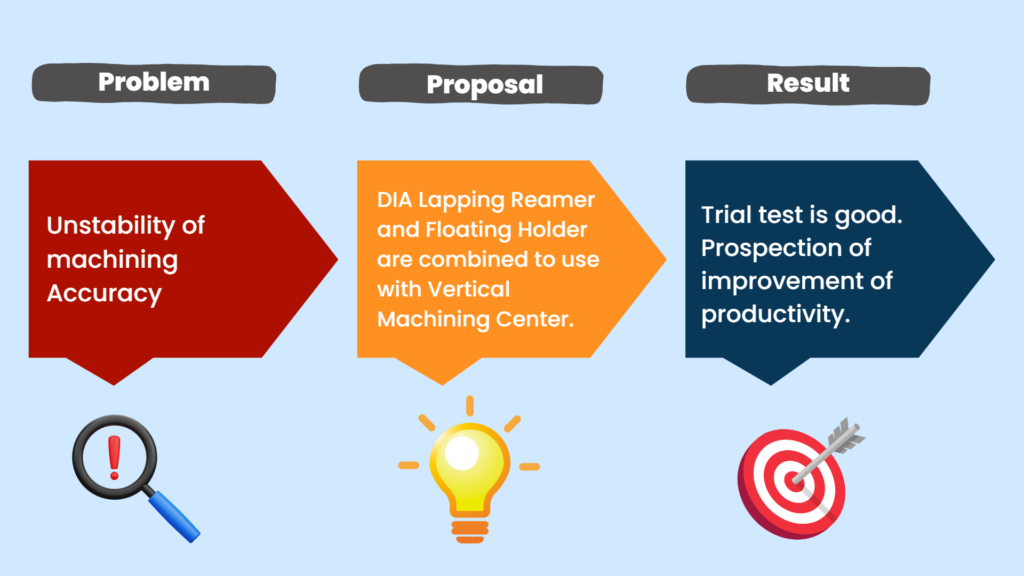
Improving the productivity of small-lot hydraulic parts (Construction machinery manufacturers)
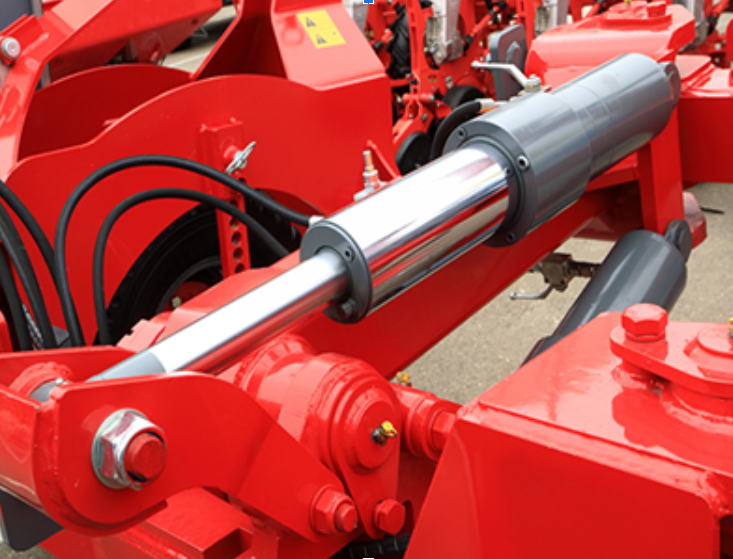
This is an example of how we improved the inner diameter finishing process of hydraulic components. With conventional surface pressure honing, it took too long to change the set-up, and since it was a small-lot production part, we didn’t want to invest in a dedicated honing machine.
So we proposed a one-pass honing method using Takezawa Seiki’s diamond reamer on a general-purpose machining center.
Thanks to this proposal, we were able to perform a series of one-chuck processing, which significantly reduced setup time and eliminated the need for new capital investment.
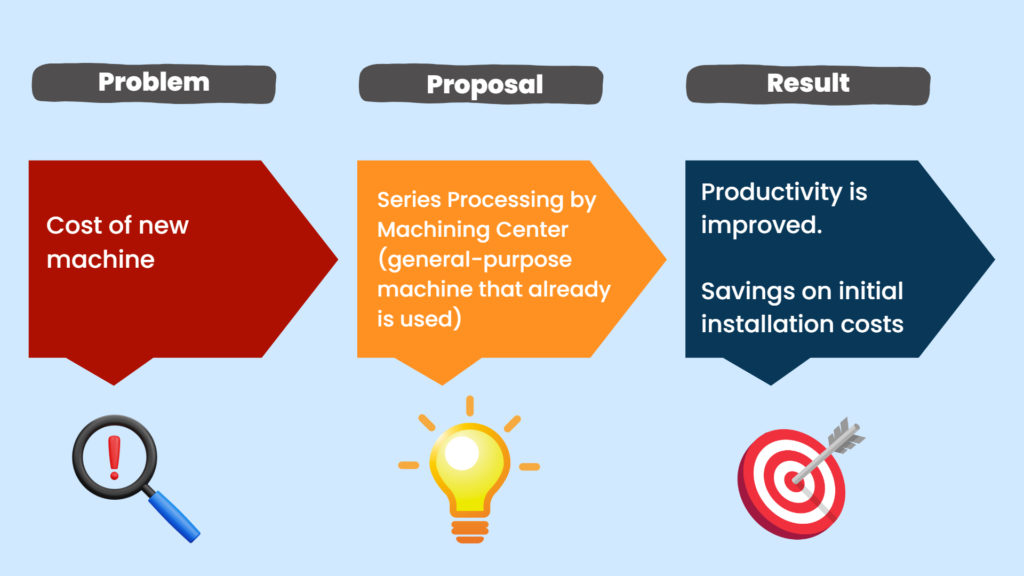
Areas of one-pass honing implementation
Takezawa Seiki’s one-pass honing has been adopted by customers in various industries.
Automotive Parts
- Turbocharger bearings
- Engine peripheral parts
- Fuel injection device parts
- Brake peripheral parts
- Transmission parts
Hydraulic Components
- Construction Machinery
- Agricultural Machinery
- Ships
- Medical peripheral parts
- Industrial equipment
Industrial Machinery Parts
- Compressor parts
- Mold parts
- Tooling
- Motor parts
- Industrial sewing machine parts
Other
- Bicycle parts
- Rifle parts
Other One-Pass Honing Contract Processing Fields
We have established long-term partnerships with customers in a wide range of industries and contribute as production partners.
Reference Web: http://www.takezawa-seiki.co.jp/reamer/onepath.html
This is reference data of the hearing from users. Actual machining accuracy and tool life may vary depending on the workpiece specifications, pre-process accuracy, machining conditions, etc.
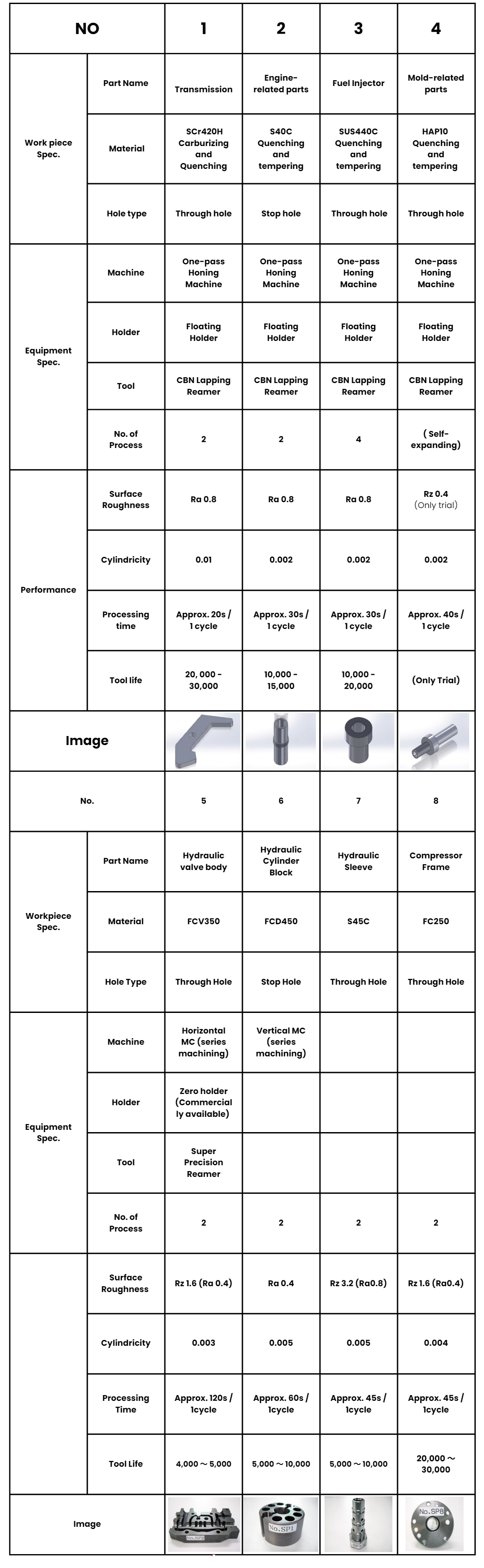