The Ultimate Honing Reamer Machine: Unlocking 100% Capacity
To overcome challenges such as tool damage and galling due to chips, as well as the degradation of machining accuracy caused by insufficient machine tool rigidity during reaming machining, honing reamers has become increasingly important. Takezawa Seiki has developed advanced honing reamer machine tools that allow for higher levels of cylindrical grinding, ultimately maximizing reamer performance. Our honing reamer products are designed to provide benefits to a diverse range of customers.
Takezawa Seiki’s honing reamer machine is equipped with an excitation mechanism that significantly enhances machining accuracy, resulting in superior precision and surface finish.
Vibrating the reamer enables the chips to be cut into smaller pieces, which are then automatically discharged. This process leads to a significant improvement in surface roughness and tool life, and enables ultra-high-precision honing.
Our innovative technology prevents the chips from damaging the tool and prevents the tool from galling by utilizing the vibration mechanism.
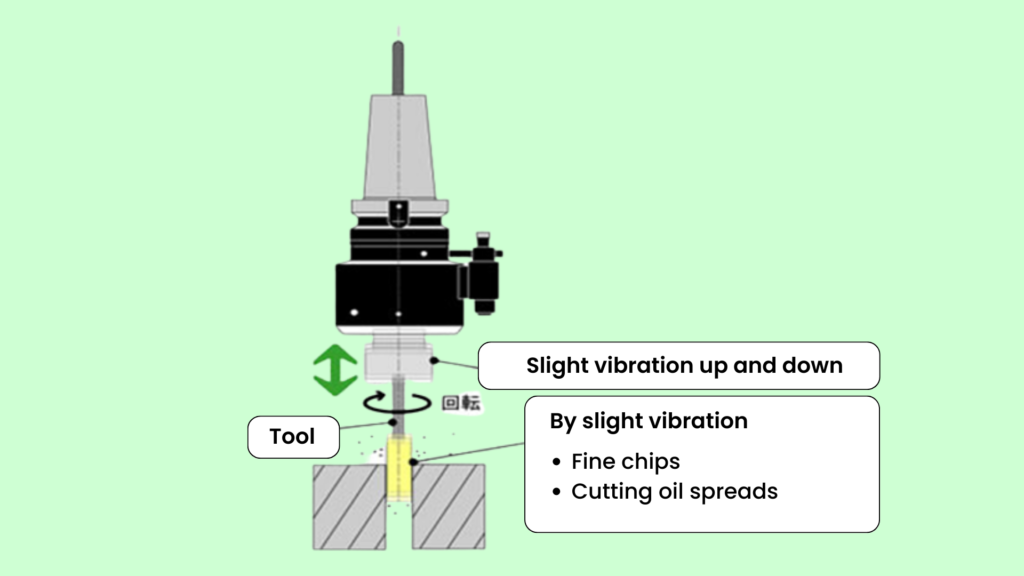
Model: THL-05 (Micron Boy)
Demonstrating our strength in small-lot, high-mix production
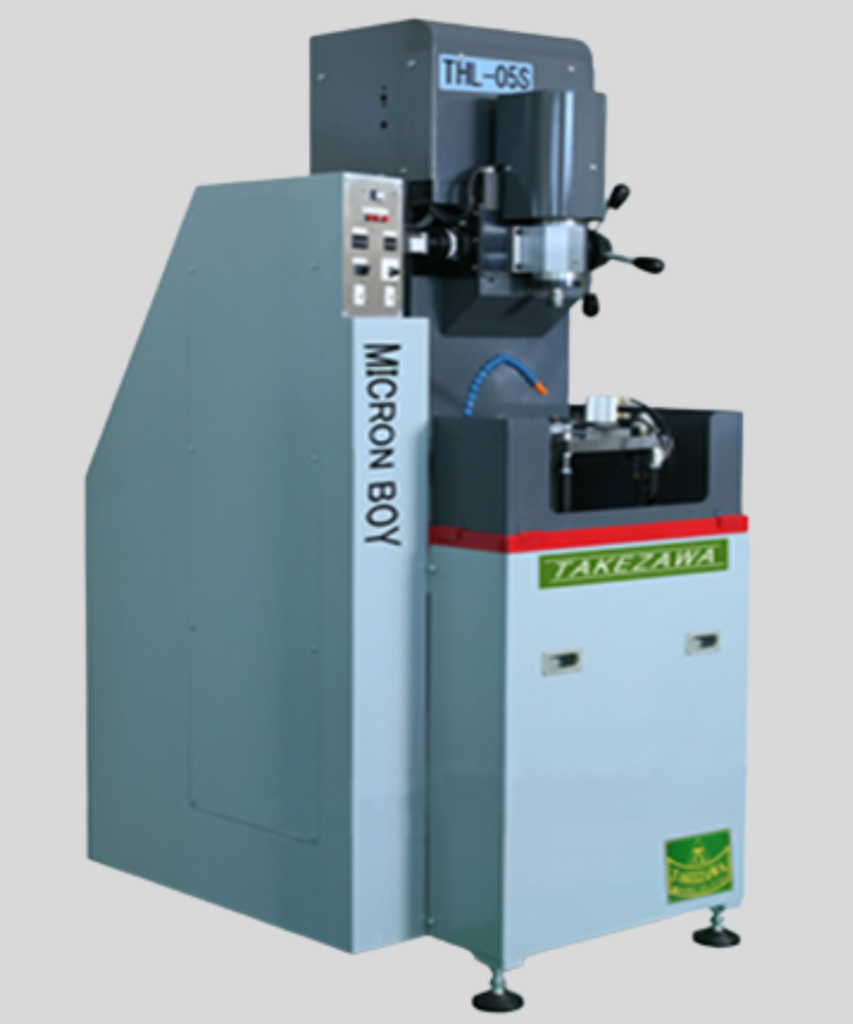
In small-lot, high-mix production, frequent setup changes can lead to a decrease in productivity. Conventional automated reaming machines require changing settings and other adjustments each time the workpiece changes, making them unsuitable for such production scenarios.
To address this issue, THL-05 adopts a unique semi-automation method that automates only processes related to machining accuracy, while allowing flexible human intervention to accommodate variations in workpiece shapes.
By combining the precision of automation with the adaptability of human workers, THL-05 achieves high productivity in small-lot, high-mix production.
Ease of use that can be quickly learned even if you have no machining experience.
The THL-05 is designed for ease of use and does not require skilled workers. All parts related to machining accuracy are performed automatically. Once you have adjusted the knob according to the shape of the workpiece, you can start machining by simply setting the processing length and rotation speed. There is no need to acquire specialized skills like those required for operating a drilling machine, nor do you need specialized knowledge or complicated commands like those needed for an NC machine.
Less space-saving than B1 paper
The installation area is the world’s smallest class for a reaming machine, with a width of 700 mm and a depth of 950 mm.
This indicates that it can be installed in a smaller space than B1 paper.
Processing accuracy of 0.5s with one-pass honing
Combining one-pass honing with Takezawa Seiki’s honing reamer enables ultra-high-precision machining up to 0.5μm. Additionally, the spindle rotation speed can be set up to 4000 rpm, providing sufficient peripheral speed to maintain machining accuracy, even for small-diameter machining of about φ2.5.
Low implementation cost
The THL-05 is optimized for processing a wide variety of small quantity products. It is easy to use, highly accurate, and space-saving while equipped with sufficient functions. Additionally, it offers strong customer support even at the introduction cost.
We have achieved a price point that is about half that of the conventional model.
Reference web: http://www.takezawa-seiki.co.jp/machine/index.html
Promotion movie of THL05 and Diamond reamer.
Main Specification of THL-05 *
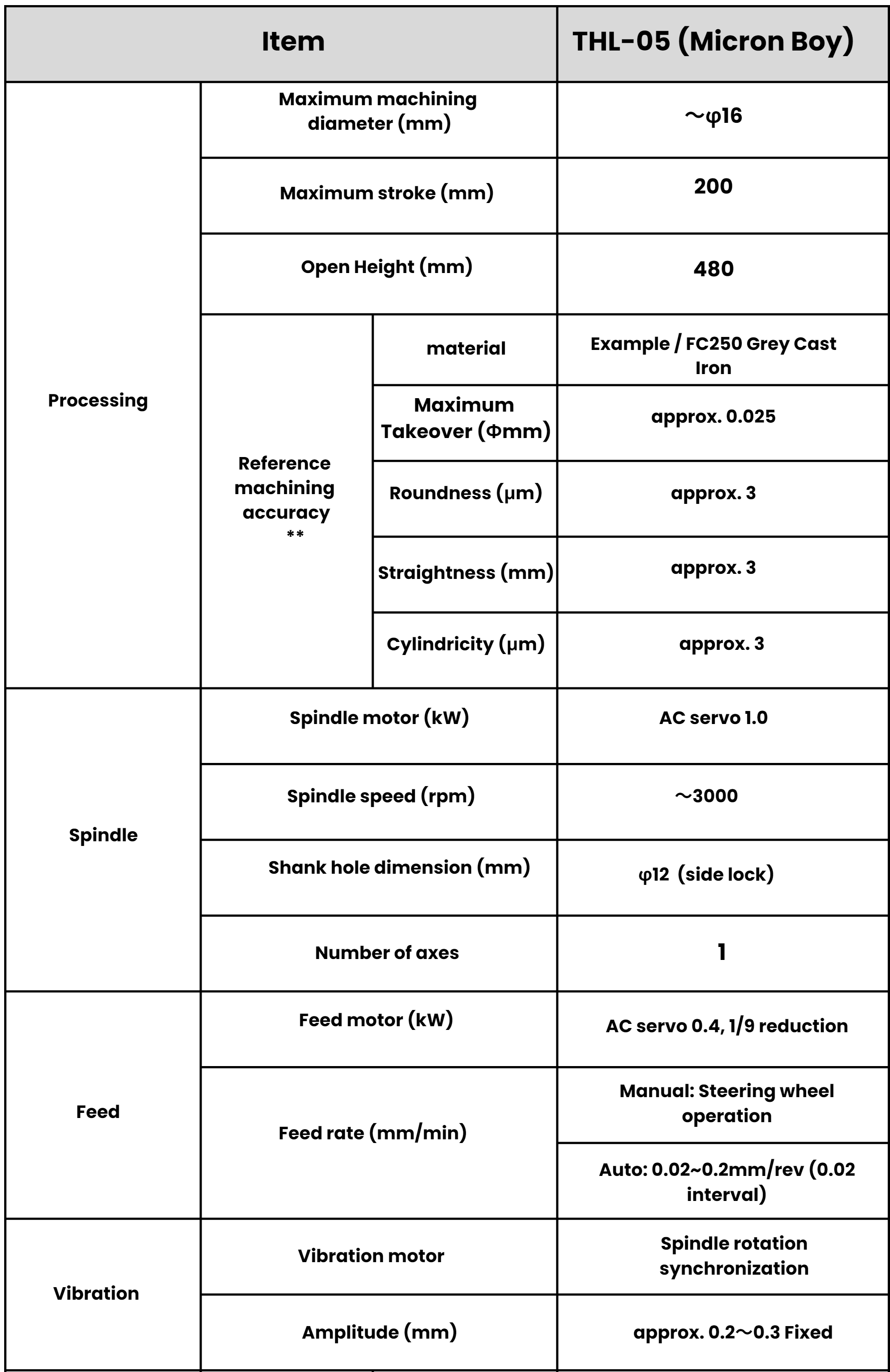
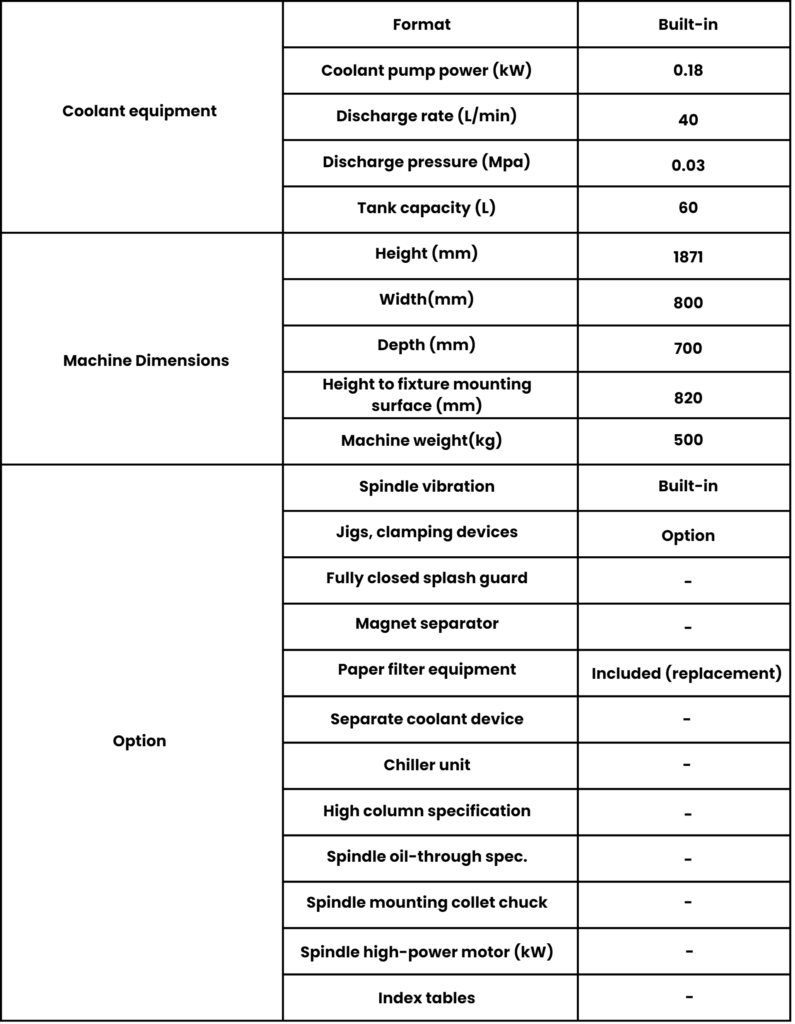
*The machine specifications may vary depending on design updates, production circumstances, and other factors.
*Actual machining accuracy and tool life may vary depending on workpiece specifications, pre-processing accuracy, machining conditions, measurement methods, and other factors
Floating Honing Holder for Better Machining and Lower Cost
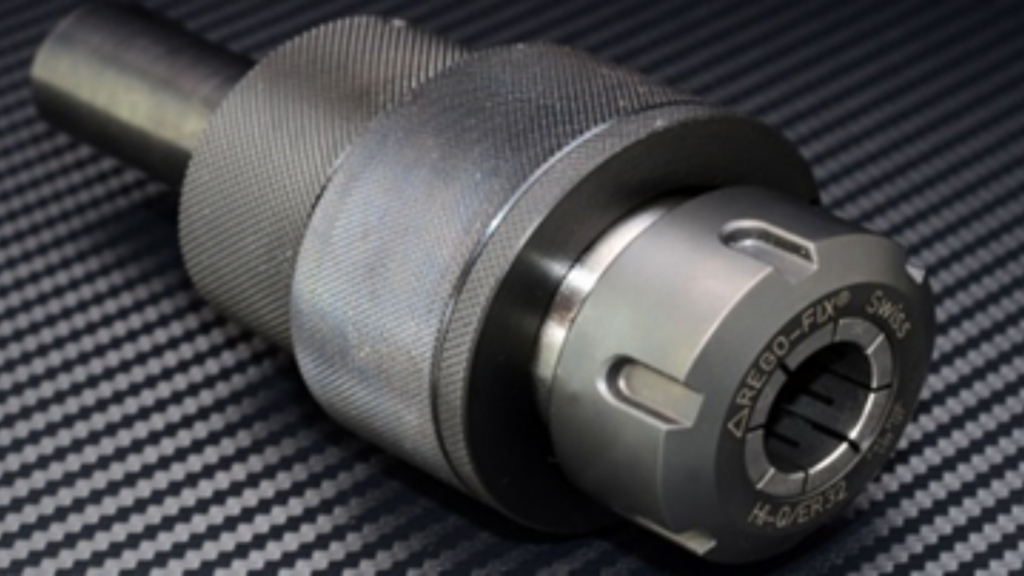
Follows even the smallest offsets.
In honing, where very high precision is required, even small deviations between the center of the tool and the center of the pilot hole can have a significant impact on machining accuracy, quality, and tool life.
Takezawa Seiki’s floating honing holder, designed specifically for one-pass honing, addresses these issues and improves machining accuracy, reduces variation in quality, and extends tool life.
Floating honing holder improves machining accuracy.
・Even if there is an offset between the center of the tool and the center of the pilot hole, the accuracy does not deteriorate, such as the enlargement of the hole diameter.
・As no excessive force is applied to the tool, it is less likely to wear or break.
・Positioning errors in workpieces and tools do not affect machining accuracy; thus, the quality remains constant.
Floating honing holders can reduce costs.
・With a small investment in the holder, higher levels of processing can be achieved than before.
・Production efficiency can be improved by reducing the number of setup hours required when changing tools.
・Lead time can be reduced through high-speed machining.
・Consistency in quality can be maintained, which leads to less rework and reduced loss due to defective products.
Method of minimizing or correcting the offset (core misalignment) between the pilot hole and the tool center axis.
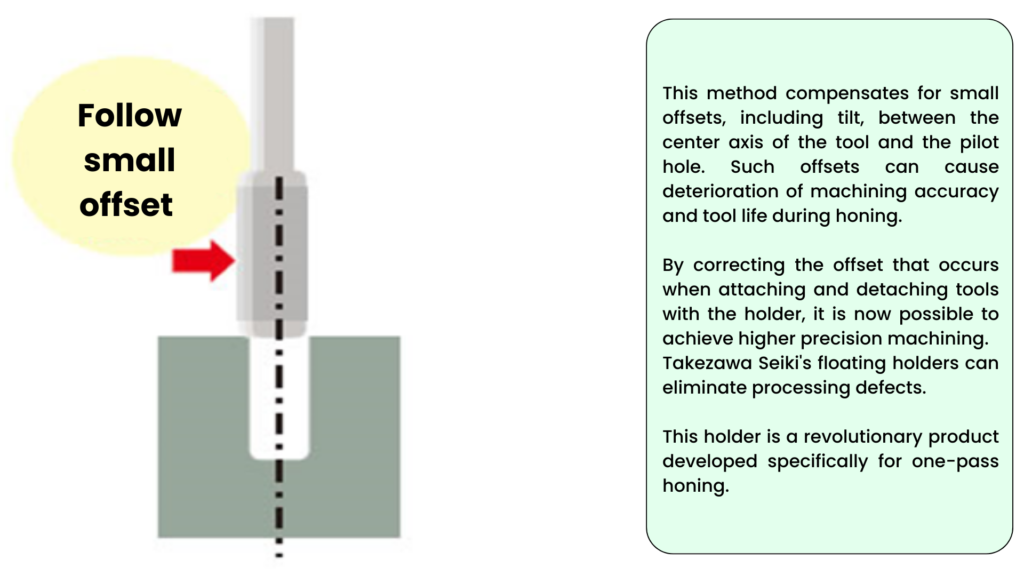
This method compensates for small offsets, including tilt, between the center axis of the tool and the pilot hole. Such offsets can cause deterioration of machining accuracy and tool life during honing.
By correcting the offset that occurs when attaching and detaching tools with the holder, it is now possible to achieve higher precision machining.
Takezawa Seiki’s floating holders can eliminate processing defects.
This holder is a revolutionary product developed specifically for one-pass honing.
Offsets that worsen machining accuracy.
In hole drilling, there is always a misalignment between the tool center and the pilot hole center.
Depending on the degree of misalignment, the machining accuracy, such as surface roughness and roundness, may deteriorate.
Moreover, as the tool is pushed forcefully into the pilot hole’s deviated position, it also experiences a load due to the reaction force from the pilot hole.
This misalignment not only degrades the machining accuracy but also results in quality variations.
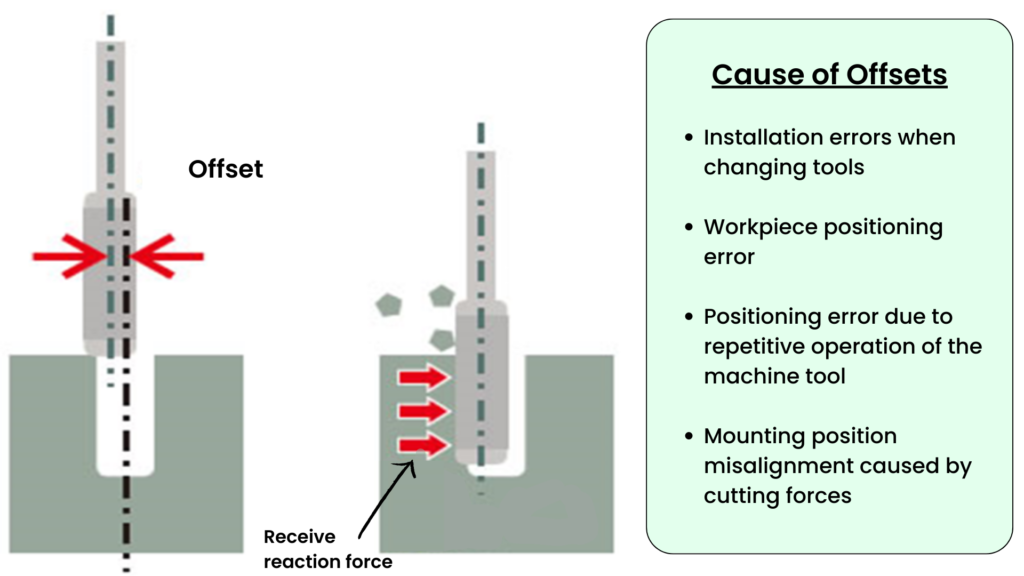
Offset correction with floating mechanism
Takezawa Seiki has developed a floating honing holder that is capable of compensating for minor deviations between the pilot hole and the tool center.
It can respond effectively to even the smallest offsets and accurately follow the pilot hole.
The honing process, which always follows the pilot hole, enhances machining accuracy, reduces quality variation, and prolongs tool life by avoiding excessive force application to the tool.
Furthermore, the characteristics of only Takezawa Seiki
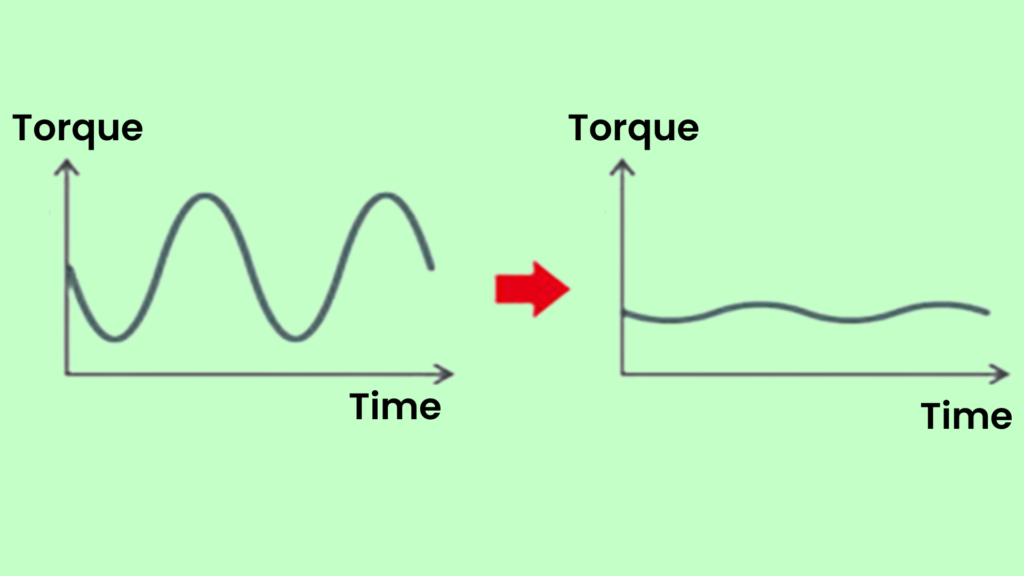
Takezawa Seiki’s floating holder maintains a constant transmission torque, unlike conventional floating holders whose transmission torque is prone to fluctuations. Such fluctuations can result in variations in quality and load on the tool.
While floating honing holders can compensate for offset-related problems, they themselves can cause other issues. However, Takezawa Seiki’s floating holder has a unique mechanism that enables it to maintain a constant transmission torque. This innovation corrects the offset between the pilot hole and the center of the tool while minimizing fluctuations in transmission torque.
Overall, Takezawa Seiki’s floating holder is a remarkable product that takes honing to the next level.
Instead of replacing your machine tool, this alone can improve accuracy, quality, and cost.
Takezawa Seiki’s floating honing holders enhance machining accuracy, quality, and production efficiency while reducing costs. Unlike conventional floating holders, the floating mechanism of Takezawa Seiki’s product accommodates slight unevenness in the positioning between the tool and workpiece, preventing uneven force on the tool.
By improving machining accuracy, quality, and cost-effectiveness without requiring customers to invest in expensive machine tool replacements, Takezawa Seiki’s floating honing holders offer significant benefits to the production line and the economy as a whole.
If you are hesitant about trying the honing process, We encourage you to give it a try at least once. You may find that it is not as difficult or intimidating as you thought.
One-Pass Honing Case Study
Takezawa Seiki’s one-pass honing can improve productivity and reduce costs in any situation that requires honing, regardless of the industry.
Inner diameter finish of Bearing parts after carburizing and quenching
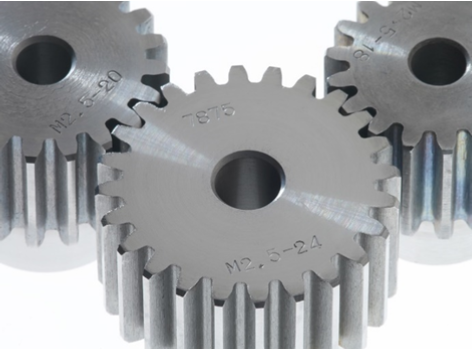
This is an example of finishing the inner diameter of a very hard material after carburizing and quenching. The heat treatment caused distortion of the inner diameter, which needed to be corrected. General tools were not efficient enough for this type of machining, so we used Takezawa Seiki’s CBN lapping reamer and floating holder. As a result, we were able to achieve the desired level of accuracy and meet our production volume.
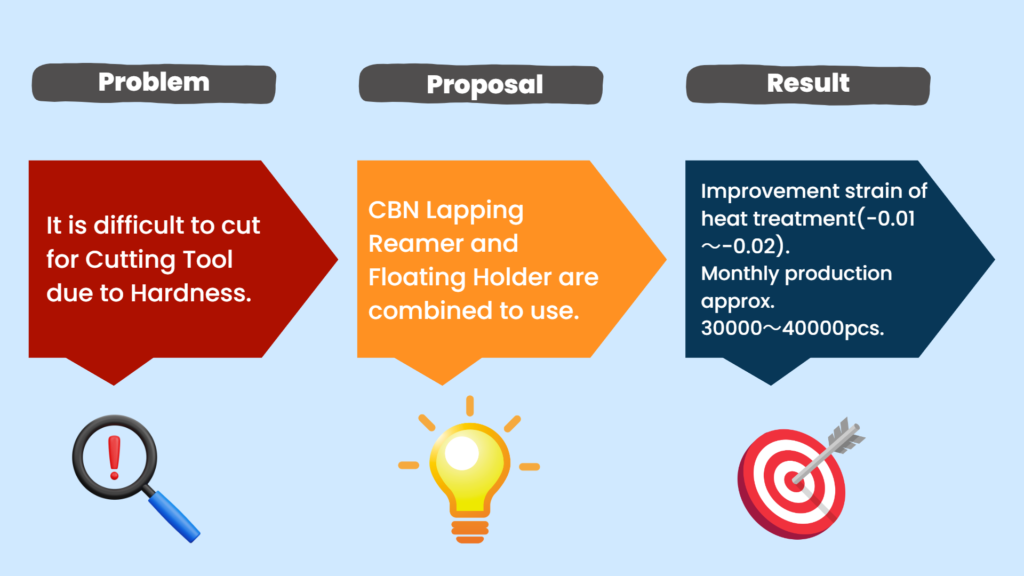
Productivity improvement through process consolidation
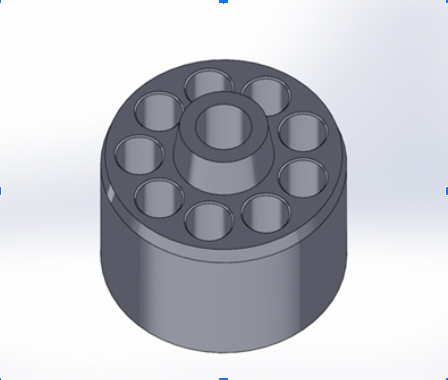
This is an example of how we reduced the time and effort needed for honing. In the past, honing was done in two separate stages: blank processing and honing. But by using Takezawa Seiki’s diamond reamer, we can now do both processes using a single machining center.
This has led to a reduction in setup time and an increase in productivity. Best of all, we achieved this process improvement without having to spend any additional money on equipment.
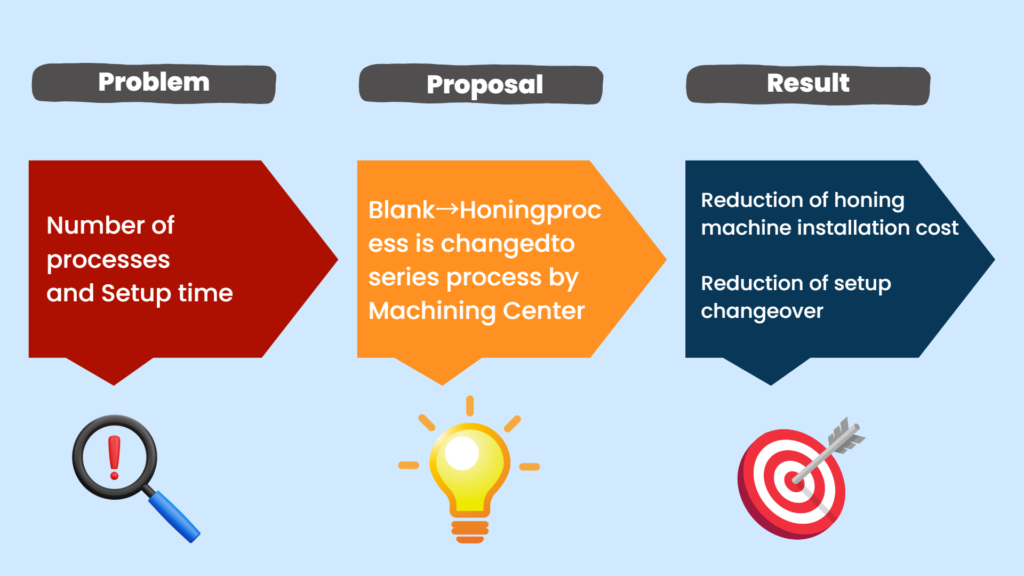
Improvement of cylinder surface roughness (Hydraulic equipment manufacturer)
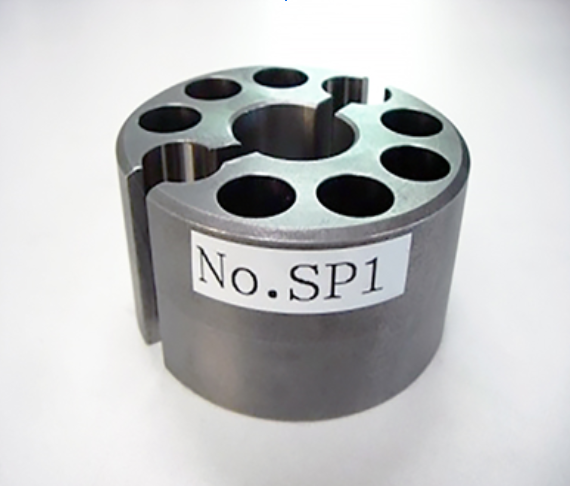
This is an example of how the honing process for hydraulic cylinders was improved. The unstable surface roughness resulted in poor yield and reduced productivity. After investigating the issue, it was discovered that the cause was the tool’s runout during processing. Takezawa Seiki proposed and provided their diamond reamer and floating holder, which were then adopted.
As a result, not only did the machining accuracy become stable, but a series of machining by the machining center became possible, reducing setup work and significantly improving productivity.
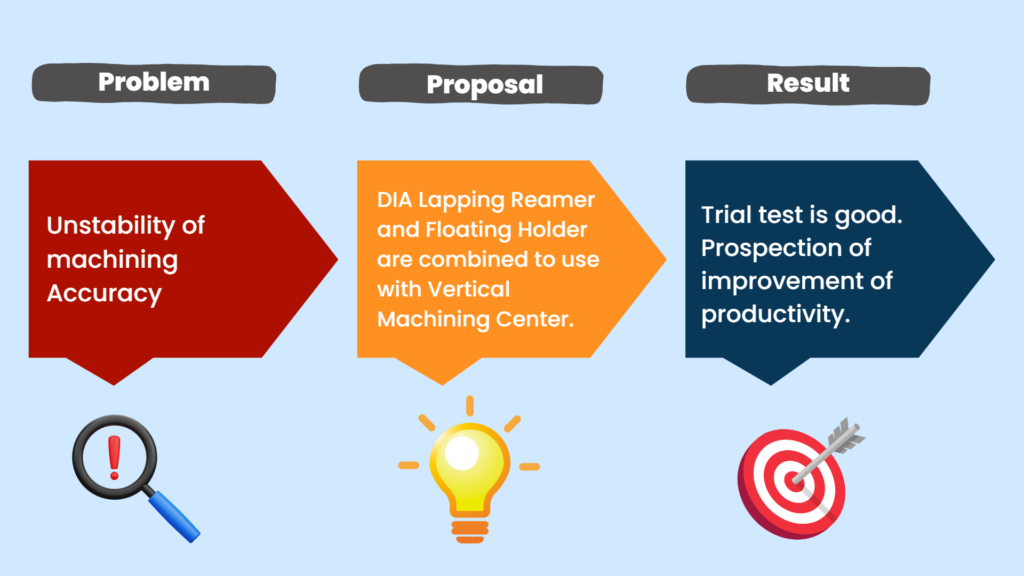
Improving the productivity of small-lot hydraulic parts (Construction machinery manufacturers)
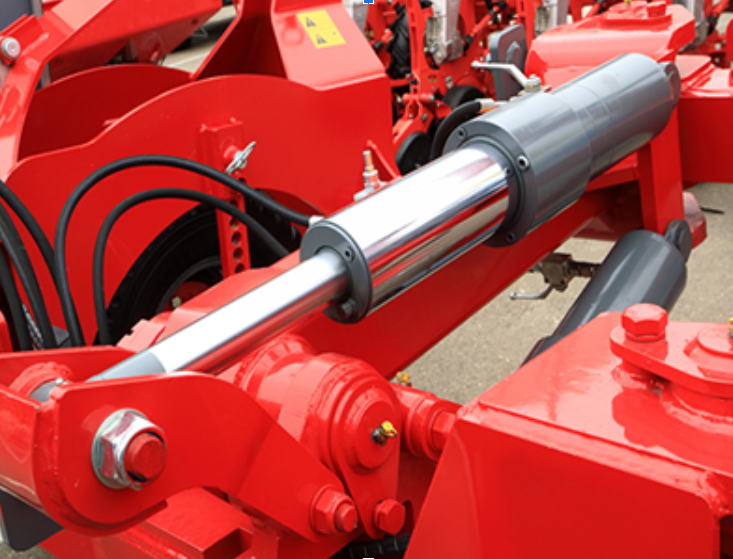
This is an example of how we improved the inner diameter finishing process of hydraulic components. With conventional surface pressure honing, it took too long to change the set-up, and since it was a small-lot production part, we didn’t want to invest in a dedicated honing machine.
So we proposed a one-pass honing method using Takezawa Seiki’s diamond reamer on a general-purpose machining center.
Thanks to this proposal, we were able to perform a series of one-chuck processing, which significantly reduced setup time and eliminated the need for new capital investment.
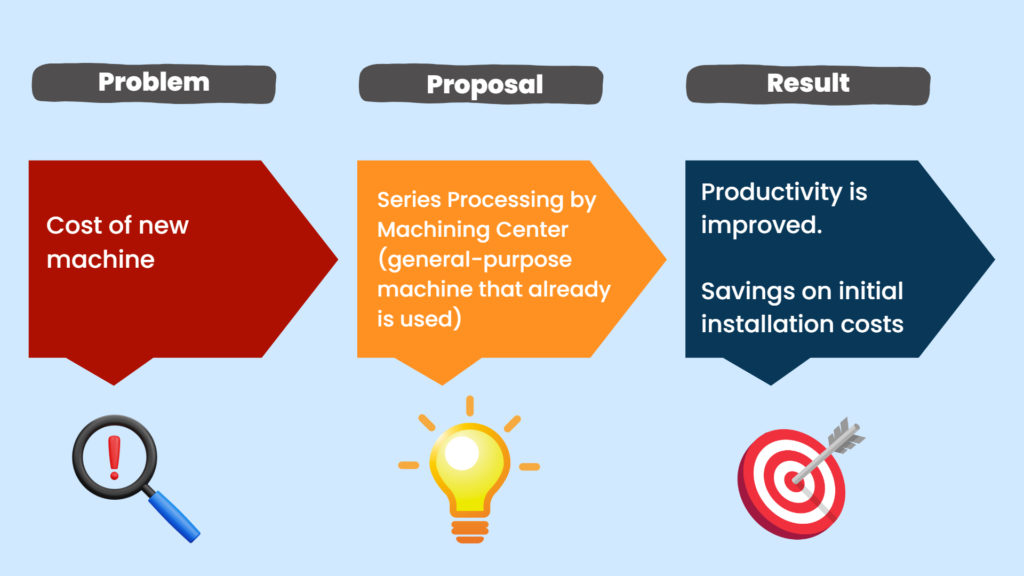
Areas of one-pass honing implementation
Takezawa Seiki’s one-pass honing has been adopted by customers in various industries.
Automotive Parts
- Turbocharger bearings
- Engine peripheral parts
- Fuel injection device parts
- Brake peripheral parts
- Transmission parts
Hydraulic Components
- Construction Machinery
- Agricultural Machinery
- Ships
- Medical peripheral parts
- Industrial equipment
Industrial Machinery Parts
- Compressor parts
- Mold parts
- Tooling
- Motor parts
- Industrial sewing machine parts
Other
- Bicycle parts
- Rifle parts
Other One-Pass Honing Contract Processing Fields
We have established long-term partnerships with customers in a wide range of industries and contribute as production partners.
Reference Web: http://www.takezawa-seiki.co.jp/reamer/onepath.html
This is reference data of the hearing from users. Actual machining accuracy and tool life may vary depending on the workpiece specifications, pre-process accuracy, machining conditions, etc.
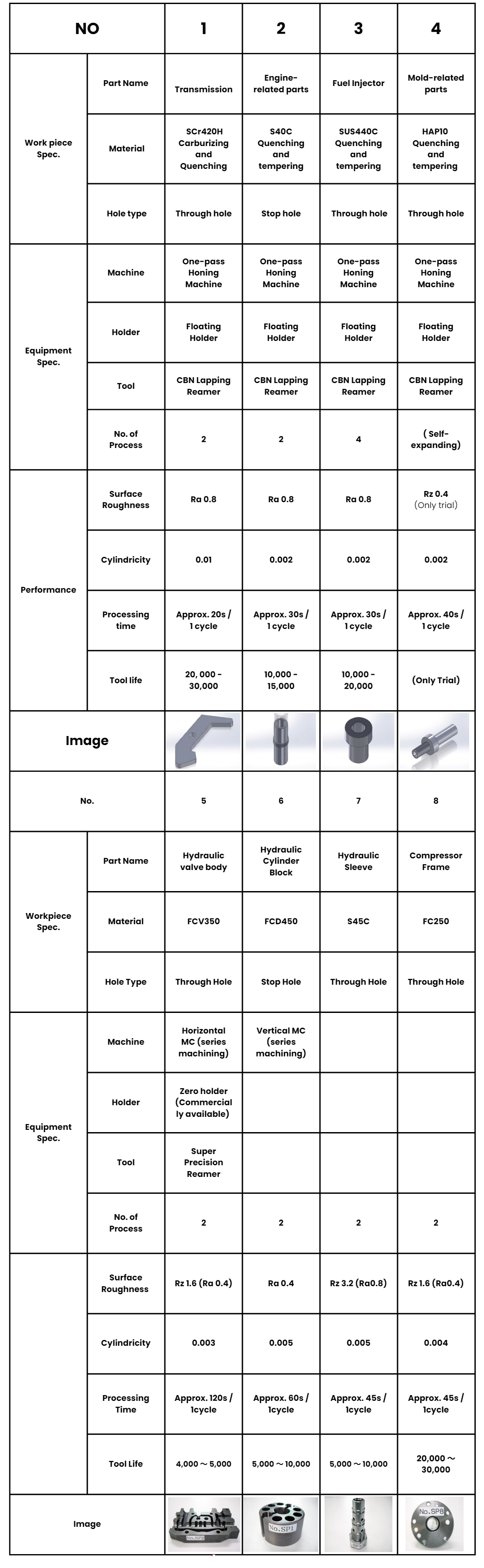
Custom Diamond Reamers by TAKEZAWA-SEIKI
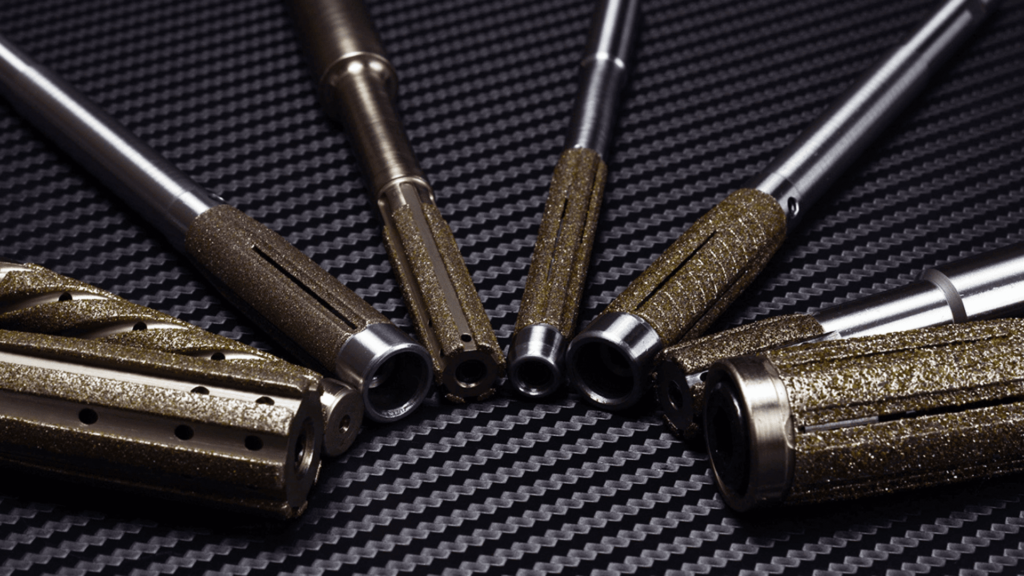
Takezawa Seiki specializes in designing custom diamond reamers that are tailored to your company’s unique needs. We take into account your workpiece, replacement, and required accuracy to create the ideal tool and process for your business. Our diamond reamers are shaped according to your specific environment, taking into consideration factors such as replaceability, workpiece shape and material, required accuracy, and tool life.
Takezawa Seiki, a professional group of one-pass honing processing, has a track record of manufacturing diamond reamers suitable for various conditions. After fully understanding and sharing the customer’s processing environment, conditions, and concerns, we propose the optimal diamond reamer. If you are thinking about improving the productivity of your honing processing line, please consult with Takezawa Seiki.
Customer-specific diamond reamer design examples
Takezawa Seiki provides different types of custom diamond reamers based on your specific needs and applications.
Expansion type
Emphasis on tool life 【 Model: DLS】
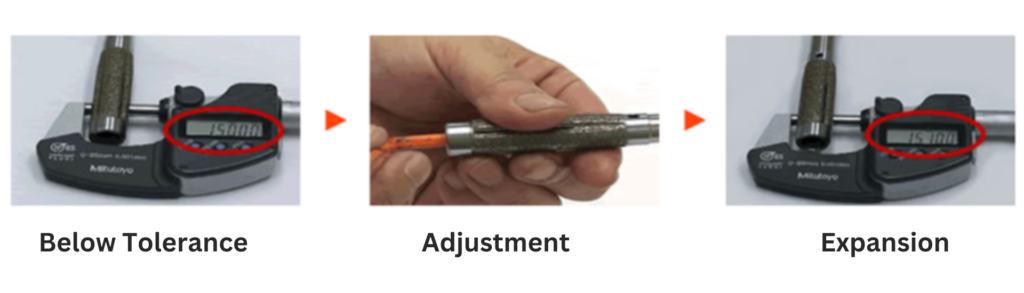
When the abrasive grains on the reamer wear out, the diameter of the reamer becomes smaller. However, it can be restored to its original size by expanding it. This means that the reamer can last 2-3 times longer than rigid reamers. Depending on the material, cost, and other factors, the reamer can usually last about 10,000 holes, and in the best case, up to 30,000 holes.
Non-Expansion type
Emphasis on tool rigidity and high precision 【 Model: SL etc. 】
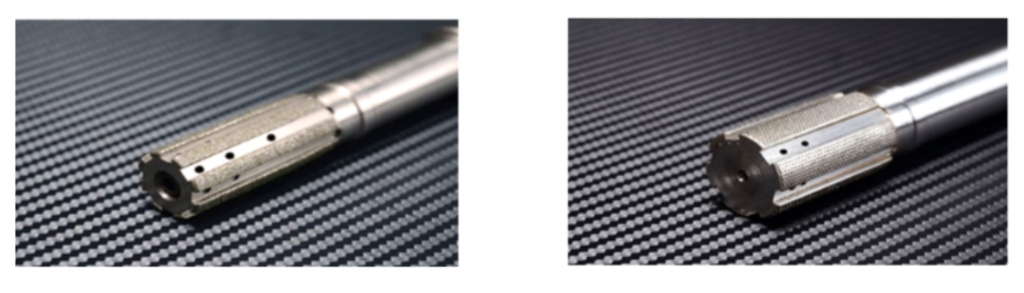
Because it is made from one solid material, it is very sturdy. This also means that highly precise reamers can be made without having to adjust the diameter separately, allowing for high-precision machining.
Horizontal machining centers
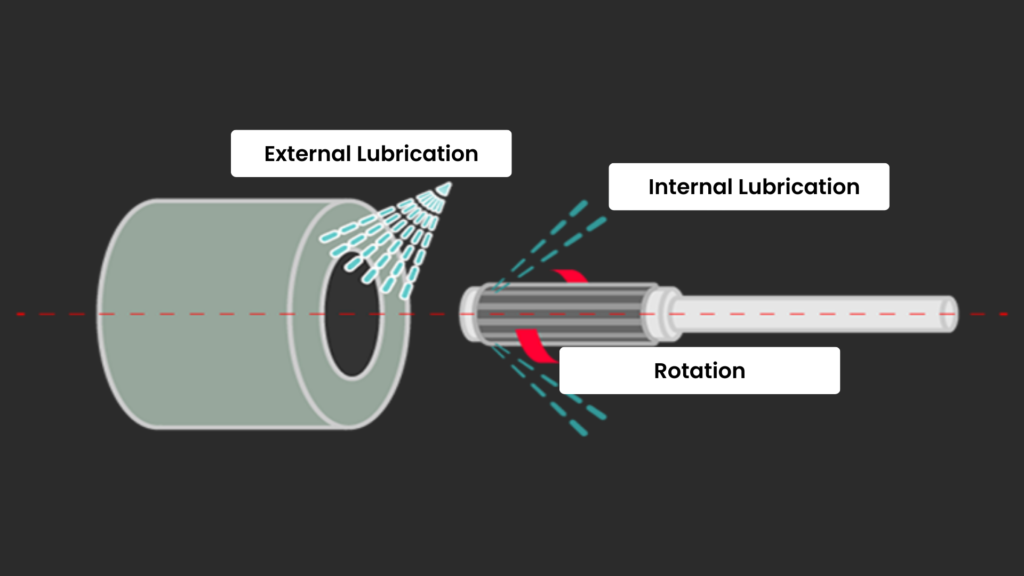
This tool can be used on many types of machine tools. Even on horizontal machining centers, it can achieve high-precision honing by adjusting for runout and using internal coolant to prevent chips from building up.
1. Sideways orientation affects tool runout. Countermeasures such as runout adjustment holders are used.
2. Sideways orientation makes it hard for cutting oil to enter. A countermeasure is to add internal lubrication through an oil hole.
We can provide detailed proposals based on the workpiece material, hardness, and replacement requirements. You can refer to the model list below for more information.
Wide Range Of Reamers
Model List
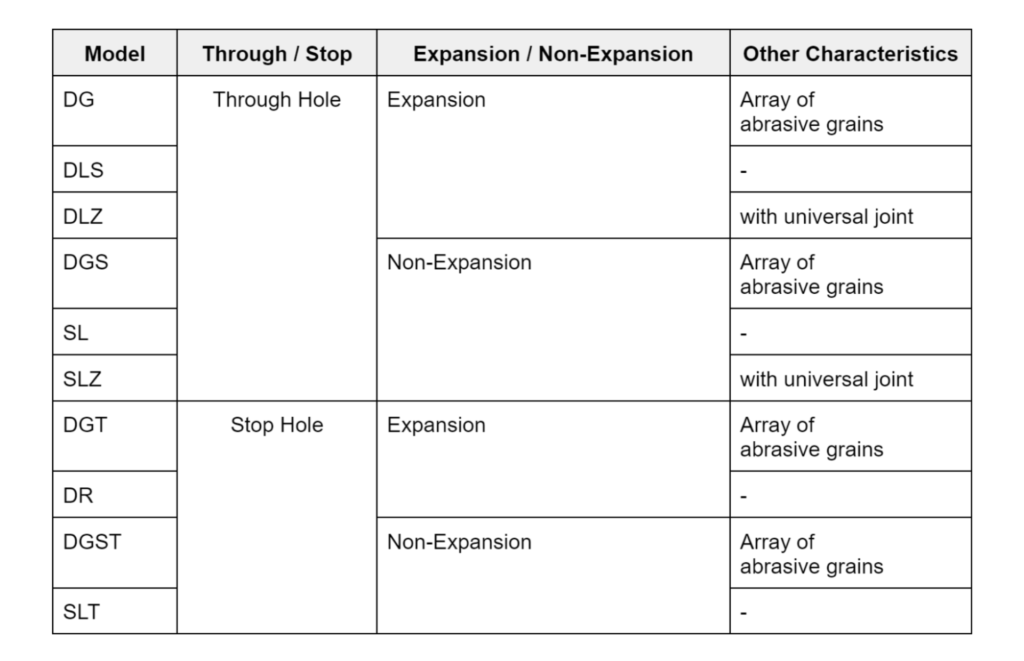
Reference Web: http://www.takezawa-seiki.co.jp/reamer/reamer.html
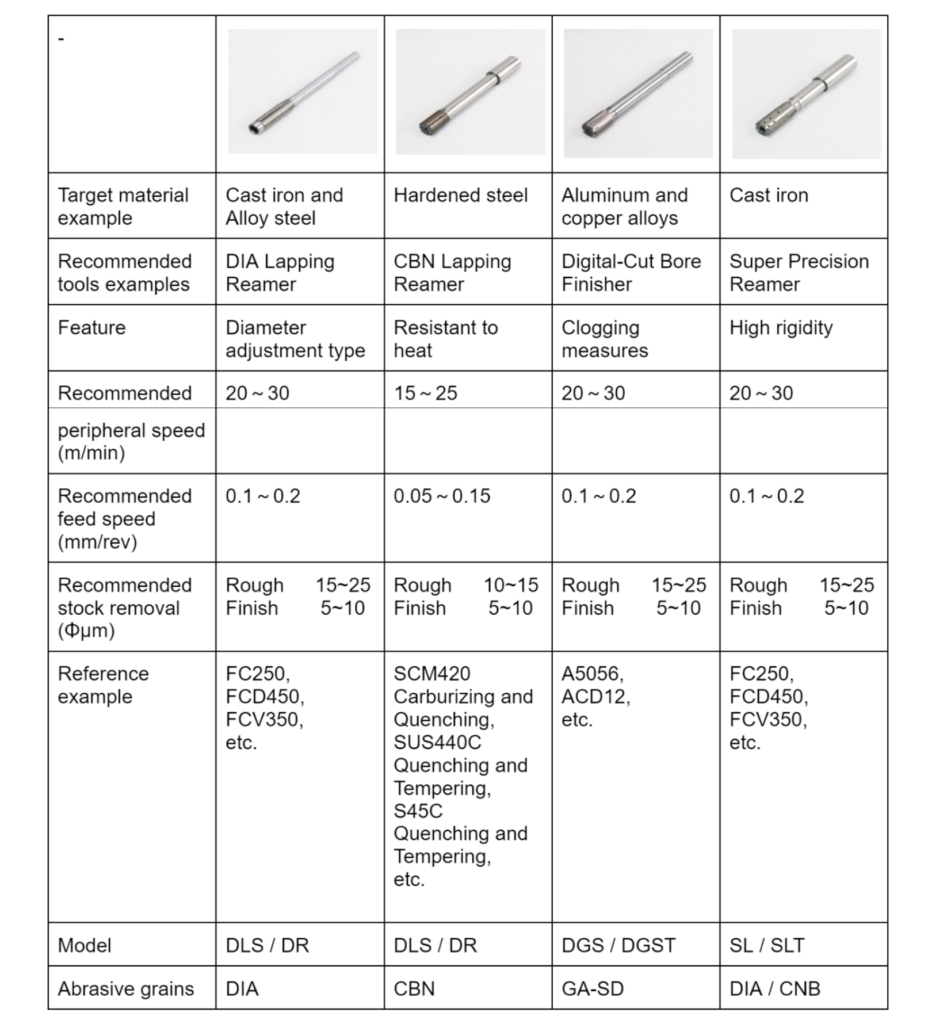
Optimize Honing with Takezawa Seiki’s One-Pass Technology
Takezawa Seiki’s one-pass honing process can take your production site to the next level. Compared to traditional honing wheel machining, it achieves both high speed and low introduction cost (*1), allowing the use of general-purpose machine tools as-is. This process is highly regarded by customers across various fields. Takezawa Seiki’s one-pass honing improves the low productivity of the honing process at a low cost. If you are interested in improving your honing process, please contact Takezawa Seiki. We also offer a dedicated processing machine (honing machine) with higher performance.
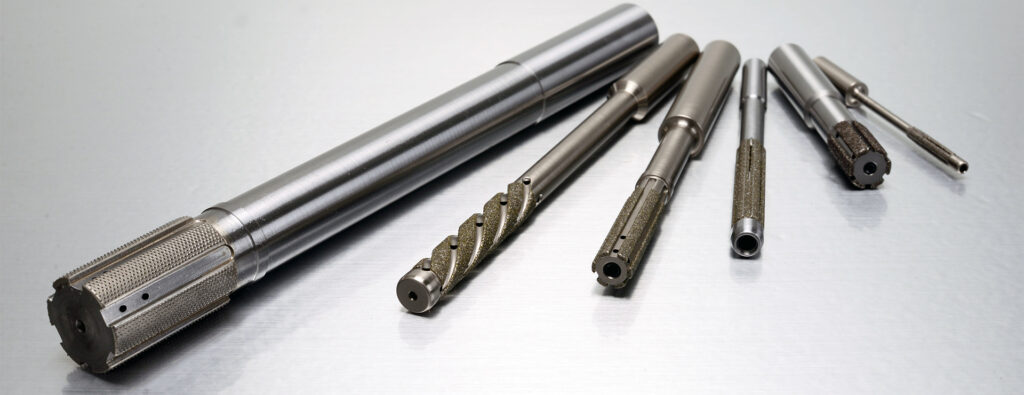
Who is TAKEZAWA-SEIKI?
Takezawa Seiki is a specialized group with over 40 years of experience in honing processing. We design and develop diamond reamers, holders, special processing machines, and a series of equipment related to honing. One of Takezawa Seiki’s unique features is our ability to solve problems from multiple perspectives throughout the honing process.
We aim to understand our customers’ problems and concerns by visiting their production sites, and then make proposals based on this understanding. Our goal is to solve problems in the way that best suits our customers’ needs. If you have any inquiries related to hole processing, please do not hesitate to contact Takezawa Seiki.
What is a Diamond Reamer?
This is an electrodeposited reamer that utilizes diamond (DIA) or CBN abrasive grains. By sharpening the workpiece with countless electrodeposited abrasive grains, the cutting force per abrasive grain can be reduced, leading to extremely high machining accuracy that is maintained consistently.
Moreover, the DIA/CBN material used in the abrasive grains has a very high material removal rate, making it possible to achieve high-precision polishing with a one-pass honing process.
What is One-pass Honing?
Takezawa Seiki confidently recommends the revolutionary grinding method of “One-pass honing”, which uses a diamond reamer to achieve ultra-high precision in a single pass for the inner diameter of a workpiece.
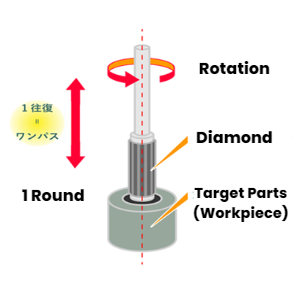
Example of proposal for One-pass Honing process design
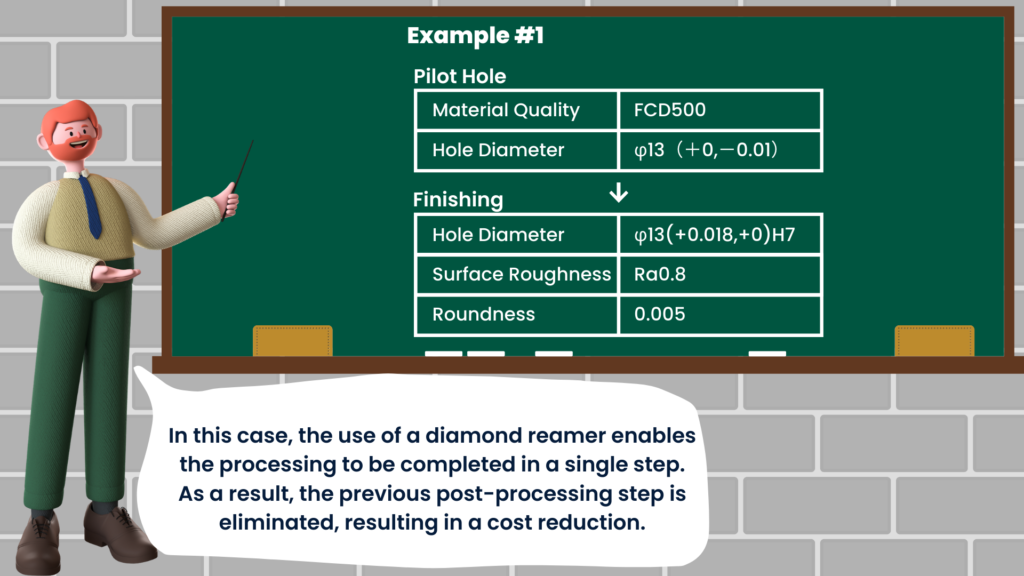
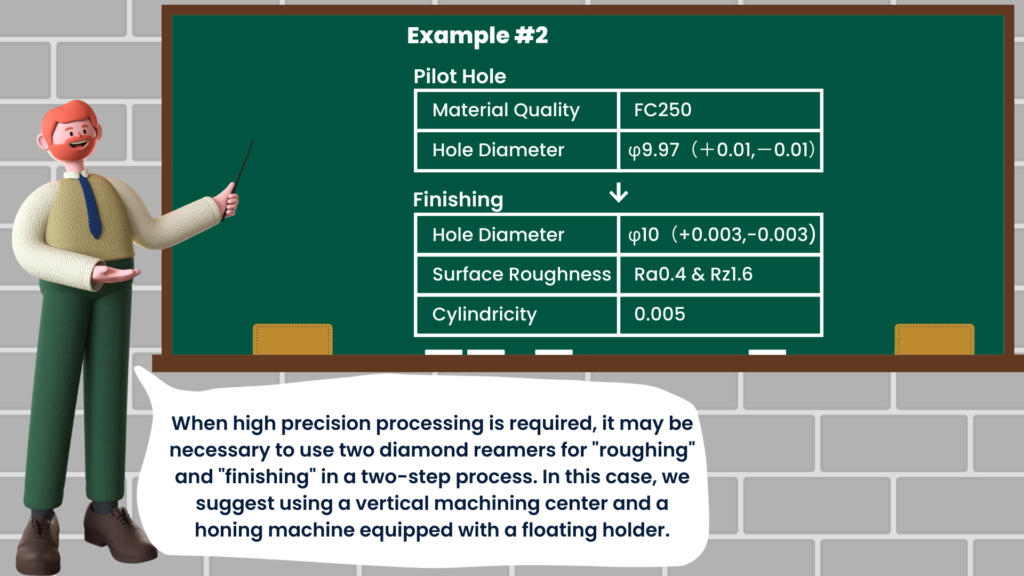
* The actual process may differ depending on the material and other processing conditions.
3 reasons why One-pass Honing is valued
The reason for this is that “one-pass honing” has the potential to achieve efficient machining that is not possible with conventional honing wheels, and eliminates the need for additional equipment investment. By using a diamond reamer with a general-purpose machining center, high-speed and high-precision honing can be achieved without the need for new capital investments.
This demonstrates the possibility of increasing productivity on your production line and achieving cost savings at an unprecedented level.
Reason 1: High productivity
Efficient process dispersion – productivity increased by more than 200%
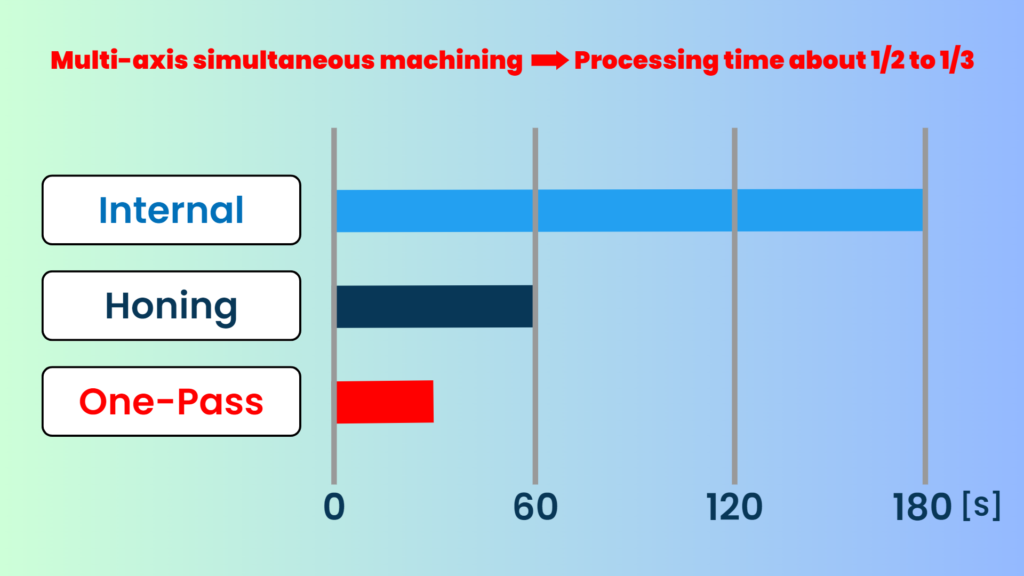
One-pass honing completes honing in a single pass, which can reduce machining time even when large amounts of material need to be removed and the process is divided into multiple steps. In some cases, our machines equipped with multi-axis mechanisms have increased productivity by over 1%. By dispersing the process, the cycle time can be shortened, and as a result, the hourly production output can be increased, leading to improved productivity.
Takezawa Seiki’s one-pass honing has the potential to significantly improve the efficiency of your production line.
*Actual machining time may vary depending on the specifications and conditions.
Reason 2: Super high precision
Fast and cheap, but super finish approaching honing whetstones.
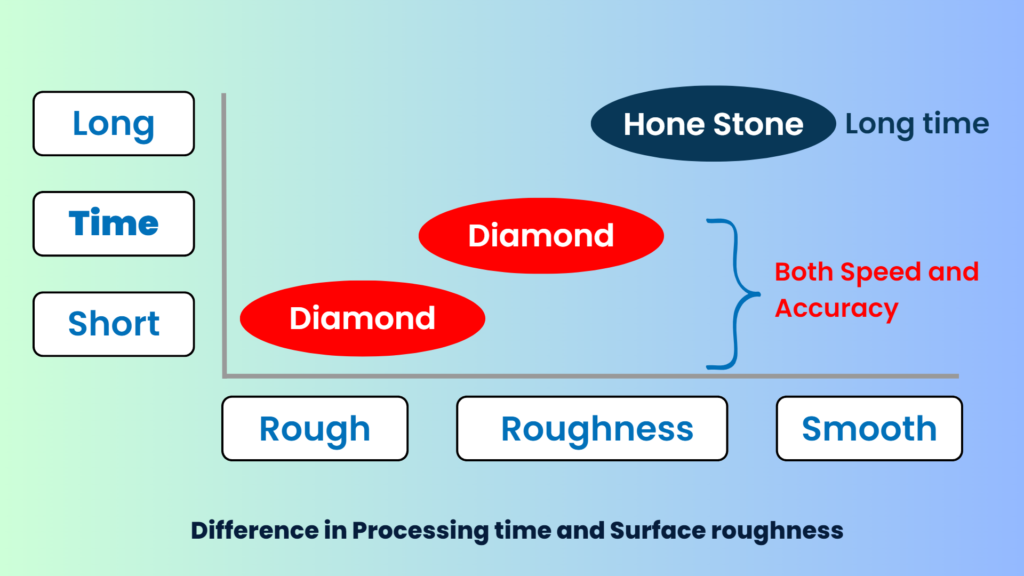
Takezawa Seiki’s diamond reamer can achieve a surface roughness of around 0.1 micrometers (μm)*, which is comparable to honing wheel machining. If you’re currently using honing wheels, consulting with Takezawa Seiki might help you improve your production efficiency and reduce costs significantly. We always put our customers first and carefully analyze how to streamline their honing process. Don’t hesitate to contact us.
*Surface roughness may vary depending on the processing conditions.
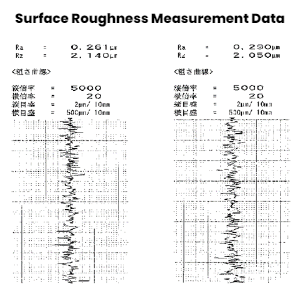
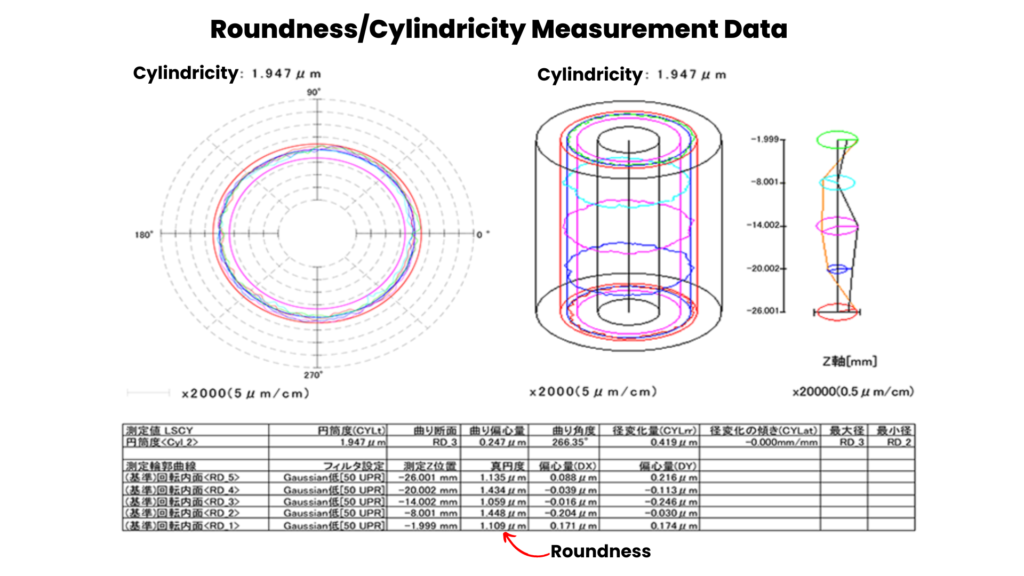
This is information based on testing and processing done in-house. The accuracy of the machining and the lifespan of the tool can vary based on factors such as the type of workpiece and the conditions of the machining process.
Reference Web: http://www.takezawa-seiki.co.jp/reamer/index.html
Takezawa Diamond Reamers
Takezawa Diamond Reamers range in size from 3/32″ (2.5mm) to 6″ (150mm). They are time-proven to deliver superior accuracy with extended tool life in demanding low-tolerance honing applications in cast iron, hardened steel, alloy steels, aluminum, bronze, brass & ceramics.
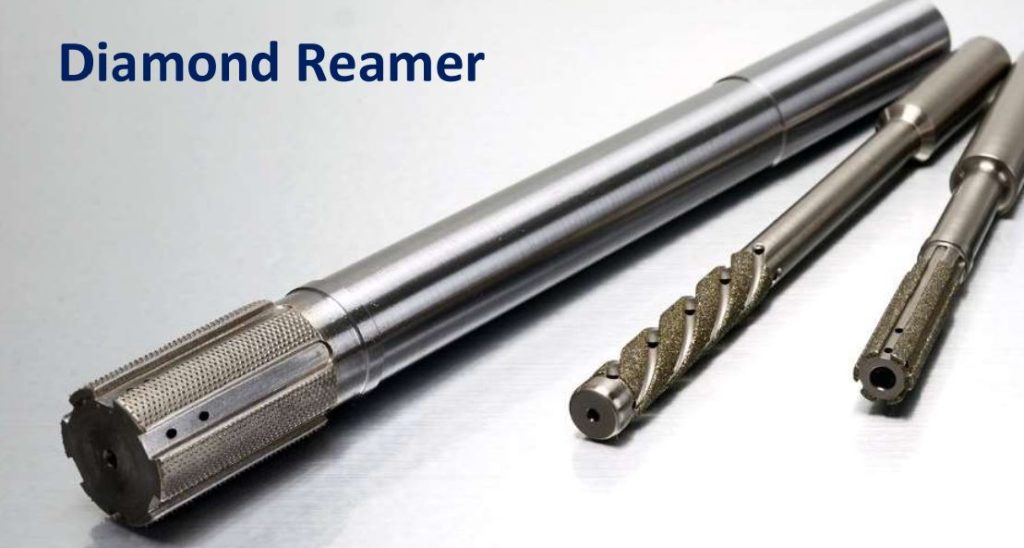
Three Diamond Reamer Models/ Reference Examples
DLS Model
1. Standard type for through holes.
2. Adjustable type.
3. The abrasive grain is DIA or CBN electrodeposition
DR Model
1. Standard type for blind holes.
2. Adjustable type
3. The abrasive grain is DIA or CBN electrodeposition.
SL Model
1. Standard type for through holes.
2. Nonadjustable type.
3. The abrasive grain is DIA or CBN electrodeposition.
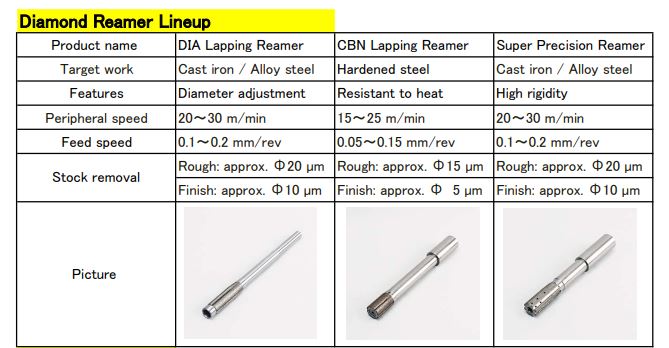
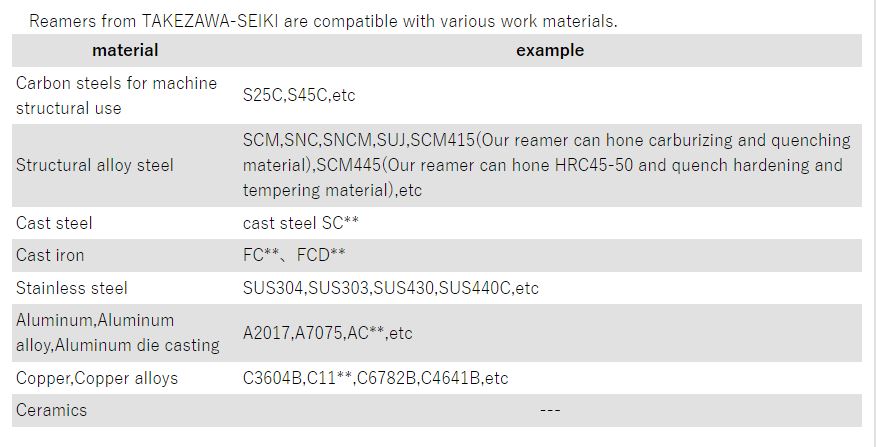